Informer | June #2
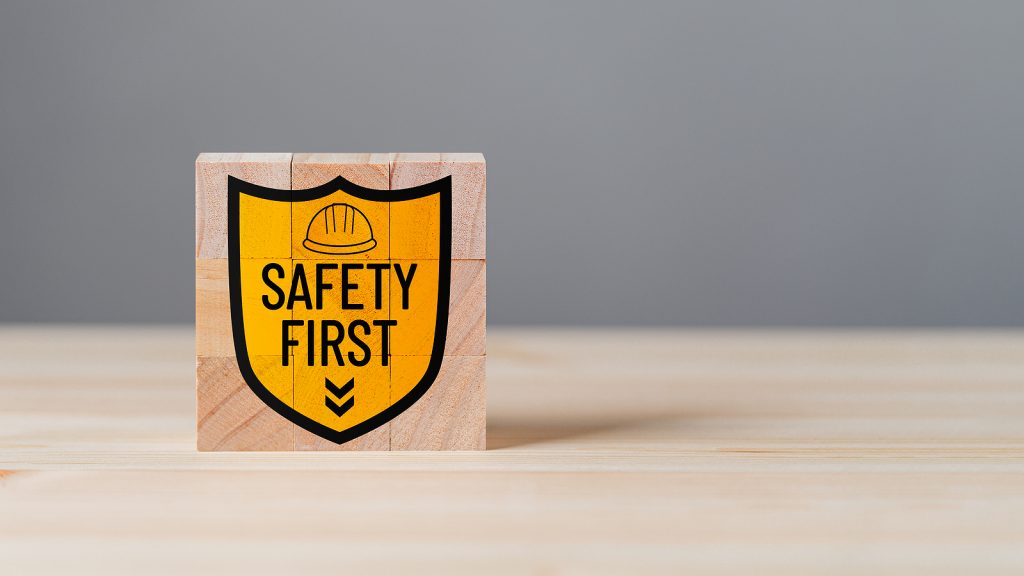
Your Safety and Risk Improvement adviser has mentioned, probably several times, to ensure employees are aware of the hazards of their jobs, and know how to correctly minimize these risks. But how do you do this? How do you ensure everyone knows what hazards exist and how to minimize them(if you cannot engineer them away)? This process is known as a Job Hazard Analysis (JHA). This is a process to analyze job tasks to identify hazards before they result in an injury. This process correlates with the worker, the equipment, the task, and the environment. These are all assessed to identify risks, and then steps are taken to reduce or eliminate the hazard.
5 Steps to Complete a JHA:
- Choose your procedure. If you are just beginning your JHA system in your workplace, you will want to focus on high-priority areas. These can be found by assessing your past claims and looking at the tasks with a high potential for an injury or a high potential for a severe injury. Additionally, those tasks that are performed rarely or are new and recently changed processes should also be a priority to be assessed.
- Break the job into steps and identify what can go wrong at each step. The easiest way to do this is to watch an employee complete the task you are evaluating; a video of these steps can also be helpful long term. You will break this down into smaller tasks (10 or fewer) so that you can evaluate these more easily.
- Identify which steps contain a hazard. Some questions to ask yourself include: are there moving pieces an employee can get into? Is there any lifting, pushing, or pulling that can cause strain? Are there slip, trip, or fall hazards? Are there environmental hazards, such as extreme temps, lighting, or noise issues? Harmful substance exposures? Any of these issues that are discovered during your analysis should be noted.
- Determine the steps to mitigate the risk of the job/hazard. These are usually done in one of 4 ways:
- Eliminate the hazard. Can you substitute your process altogether? Modify the process or tools or adapt the work environment(maybe additional ventilation).
- Contain the hazard. Would a machine guard or a booth around that particular process solve the risk?
- Revise the procedures. Adding steps or just changing the order of them could easily eliminate some hazards.
- Reduce Job Frequency. Maybe it comes down to rotating workers for certain job duties or cutting the time employees are completing certain tasks.
- Communicate the findings. Once you have decided on the process to reduce hazards, these new processes/procedures should be communicated to all affected employees. You will also want to refresh employees routinely, especially for jobs that are rarely performed.
A JHA should be treated the same as all other processes and procedures. They should be reviewed and updated regularly to ensure changes are truly for the benefit of employees, and that there was a reduction in hazard. Also, you will want to review and update any time there is a near miss or incident, or equipment changes.